- Series production of the Chiron in Molsheim gathers pace
- The first vehicles are to be delivered to customers in the first quarter of 2017
- Up to 70 Chirons are to be built in the Bugatti Atelier in 2017
- On average, six months pass between start of production and delivery
- 20 employees assemble the Chiron from over 1,800 individual parts in the Atelier
- Unlimited customising opportunities with respect to materials and colours
- The world's most powerful, fastest, most luxurious and most exclusive production super sports car is completely hand-built and is subject to the most stringent quality controls
- Chiron production is 'Haute Couture de l'Automobile'
- Extensive modifications to the Molsheim facility for the Chiron
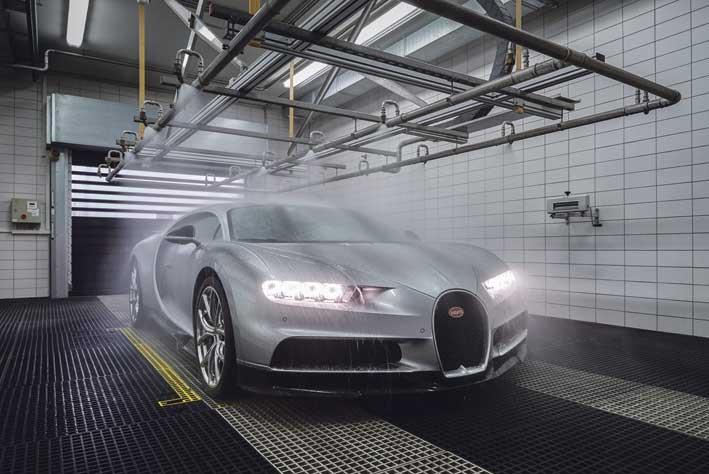
Series production of the Bugatti Chiron is rapidly gathering pace. Currently, 12 super sports cars are taking shape in the French luxury brand's production facility, the so called "Atelier" at the company's headquarters. It is planned to deliver the first vehicles to customers in the first quarter of 2017 and to build up to 70 of these cars this year. On average, about six months pass between the start of production and the delivery of a Chiron. 20 employees in the Atelier assemble the world's most powerful, fastest, most luxurious and most exclusive production super sports car from more than 1,800 individual parts, working solely by hand.
The Chiron is subjected to the most stringent acceptance tests and quality controls before it is delivered to the customer. Many modifications to the facility at Molsheim were made for the assembly of the 1,500 PS super sports car to take account of its higher performance and the generally more complex nature of the new product and its production process.
At its facility in Molsheim in an idyllic location in Alsace, which has been the home of the marque since it was founded in 1909, Bugatti is making automobile dreams come true with the Chiron. Before customers can take delivery of their new Chiron, there is a lot to do. The first step is the configuration of the vehicle, which is completed by the customer together with a designer from Bugatti. Each Bugatti is unique and is manufactured in accordance with the customer's personal wishes. This is why personalising is a top priority for Bugatti. 23 topcoat colours and eight carbon variants form the basic range for the exterior. In the interior, customers can choose from leather in 31 different colours or Alcantara in eight colours, as well as 30 stitching, 18 carpet and 11 belt colours. In addition to this basic range, thousands of other colours are possible. And in addition to that, individual colours may even be created to match a favourite handbag or the label on a customer's preferred brand of mineral water. There are also many other design options such as logos or initials on the bottom of the rear spoiler or embroidery on the headrest and leather inlays on the central console. With its customising program "La Maison Pur Sang", Bugatti is virtually in a position to meet a customer's every wish - provided that installation in a super sports car is technically feasible and meets Bugatti's high quality requirements. Only when the customer has signed off the configuration does production planning start. The many small wheels of a complex process that runs to a strict time schedule are then set in motion. At the end of this process, a Chiron leaves the Atelier in Molsheim. Normally, a Chiron takes about nine months for this journey from configuration through to delivery - with an average degree of customising. The more unusual a customer's wishes in terms of materials, colours or other details are, the more time will be required. When a production slot has been assigned to a customer's vehicle, the parts that are needed are ordered. From now on, the countdown has started and it will take about six months up to the delivery of the car. Now, Bugatti's suppliers, who are located throughout Europe, work hard to deliver the parts that are needed to Molsheim in time for assembly.
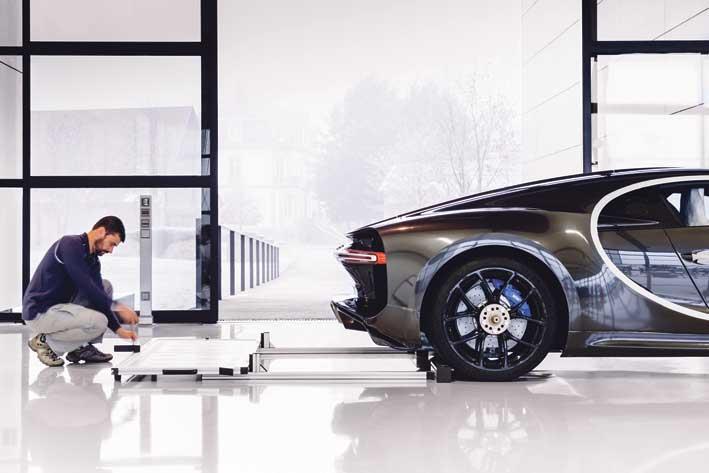
One month before the start of production in Molsheim, the bodyshell is assembled with the monocoque and chassis substructure for the first time to ensure that everything fits together perfectly. Each part is assigned a kit number and is then transferred to the paint shop. It takes about three weeks to apply the various coats of paint. In the case of visible carbon fibre, a field in which Bugatti is the market leader in terms of production quality and diversity of colours, six layers are required. For the top coat, up to eight layers may be needed depending on whether the finish that has been ordered is uni, metallic or pearlescent. The process is so time-consuming because all layers are applied by hand and each individual coat needs to be sanded down and polished before work can start on the next coat. Then the starting signal is given for the assembly of the Chiron in Molsheim. Christophe Piochon, Member of the Bugatti Board of Management responsible for Production and Logistics, watches over production, making sure that all processes run smoothly and there are no hitches. "Here in Molsheim, we have a small factory with a small warehouse. Neither our equipment nor our procedures can be compared with those of other car plants," says the 40-year-old mechanical engineer, who worked in quality assurance with the Volkswagen Group before joining Bugatti. "'Just-in-time' has a very special dimension for Bugatti," he adds.